Welcome to our overview of the importance of Leadership in Process Safety. In chapter 2 of this series, we looked at the broad issue of Process Safety Management in major hazard sectors, with particular reference to the UK’s regulatory guidance framework, namely HSE’s Major Hazard Regulatory Model.
Within the leaflet produced by the Health and Safety Executive, entitled The Major Hazard Regulatory Model, they provide an overview of Hazard Management which they term ‘The Big Picture’.
The Five Key Areas of The Big Picture
1. The first group is about leadership. Recognising the major accident hazards, how control could be lost and the outcome of this, is fundamental within Hazard Management Leadership. This also incorporates Plant, Process and People and the Major Hazard Control Measures or Barriers that can be deployed to prevent and mitigate. More on these Barriers later.
2. In the second stage we need to identify the hazards. This is a critical aspect of this process, if we don’t identify the hazards, we cannot assess the risk or control it. Within this, we need to understand the Hazardous Property Conditions and Volumes of Material, the Stage in our Plant Lifecycle where this could occur, as well as the types of activity we are undertaking.
3. The third element looks at how we assess the risks. This includes looking at Challenges to Integrity, the consequences of this loss and the probability of it occurring. With this information we can Risk Profile the task.
4. The fourth section is about determining suitable Control Barriers to Prevent and Mitigate the hazard. These Barriers will involve elements of Plant, Process and People.
5. Finally the fifth part will focus on Checking, Measuring and Reviewing. This helps to ensure controls are working as intended and investigates any Failures or Incidents.
Altogether, it looks like this.
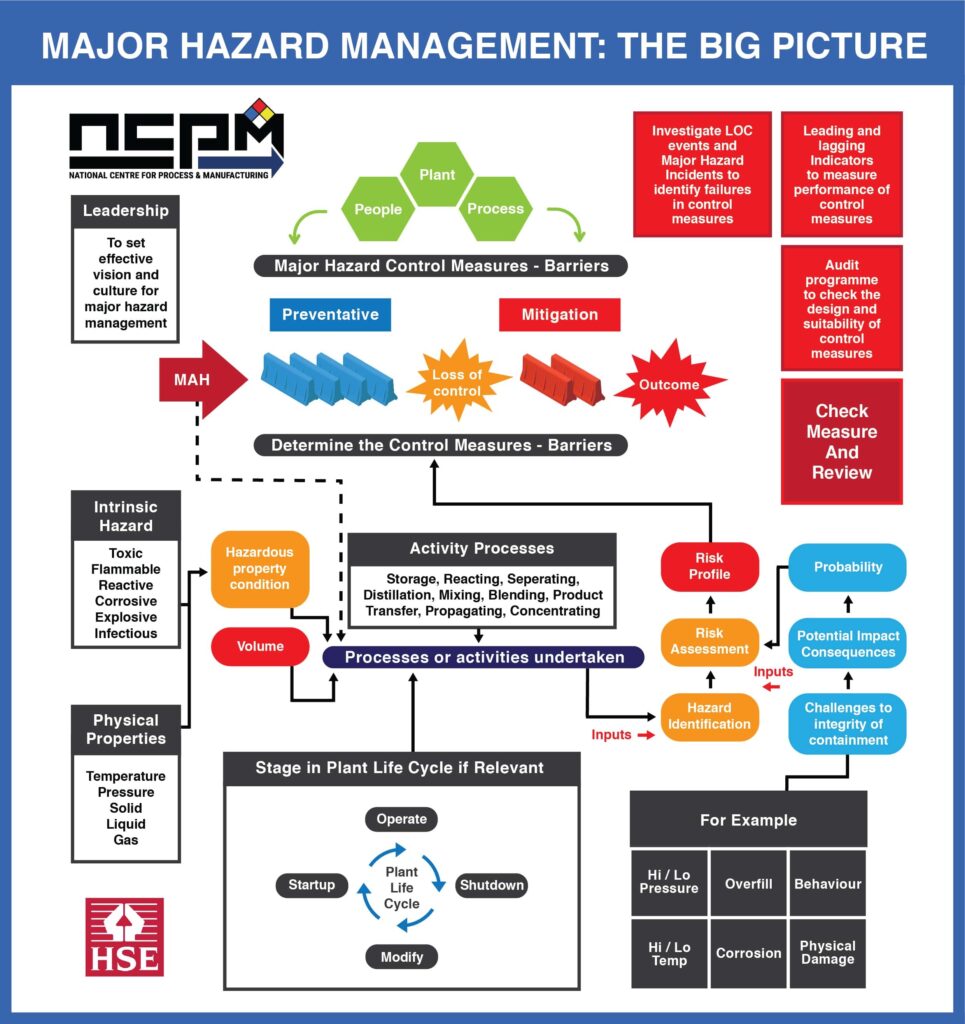
Now, let’s look in more detail at the first of those key areas – Leadership:
Leadership in the Major Hazard Regulatory Model
Process Safety Management Systems and arrangements, plus their supporting organisational safety culture, cannot be sustained without effective leadership. The multi-layered arrangements needed to manage Major Hazard Risks need to be delivered and maintained by managers with vision and determination.
This cannot be left as the sole preserve of safety specialists within an organisation. It involves the entirety of the Plant, the People and Process.
Embedding and delivering best practice is something that needs to take place within every tier of a business.
If this doesn’t happen, there can be a cultural failure to complete the circle of Process Safety and thus erode the multi-layered barrier system that has been built.
Leadership is crucial to the effective function of the Major Hazard Regulatory Model, which is true within our sector and across all the high hazard industries.
Jo Nettleton, Deputy Director and Head of Radioactive Substances and Installations Regulation at the Environment Agency gave a presentation to the Hazardex 2019 Conference, in which she referred to:
“ … the absolutely vital need for leadership and collaboration across the major hazards community – in its widest sense; within sectors, across industry, with government, regulators, NGOs and the public.”
Here at Reynolds Training, we could not agree more.
The Process Safety Leadership Group (PSLG)
The Buncefield incident and subsequent investigation resulted in a raft of recommendations from the Major Incident Investigation Board (MIIB) and Buncefield Standards Task Group (BSTG). The latter led to the creation of the Process Safety Leadership Group (PSLG), formed by the industry with a wider commitment to provide positive action and results based on the recommendations, which have continued to be steadily implemented.
One of the outcomes of the PSLG was recognition of the critical role that industry leaders have to play in relation to Process Safety Management, leading to the development of the PSLG’s Principles of Process Safety Leadership. These principles have recently been further underpinned by the Tank Storage Association’s Safety Leadership Charter.
So, how do we ensure effective leadership on the ground?
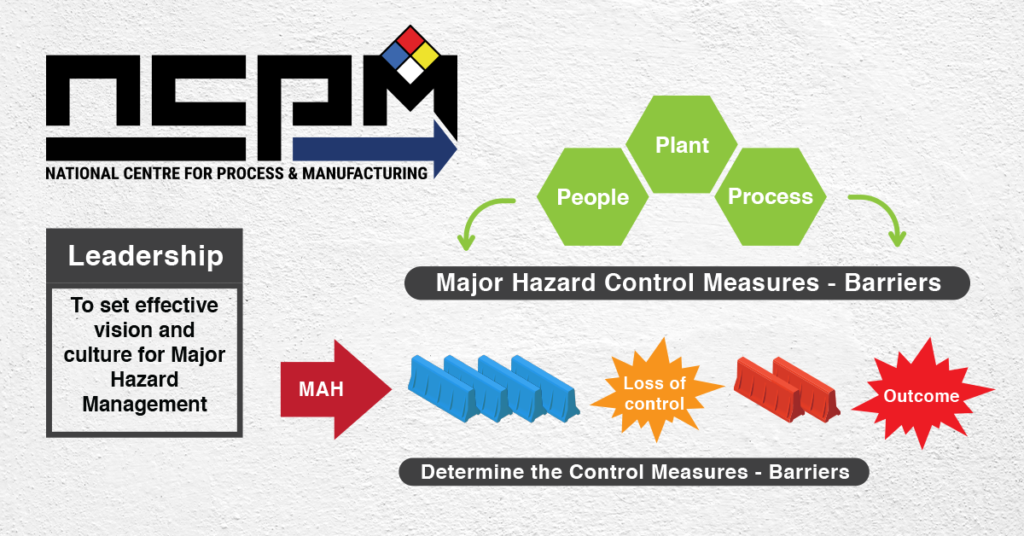
Leadership should be empowering. It should set an effective vision and culture for Major Hazard Management. Leadership’s effect on culture plays a critical and very specific role in the prevention of catastrophic failures. The challenge for organisations is defining what they need from leaders to support a culture of process safety excellence.
The Four Key Elements of an Effective Process Safety Culture
A Process Safety culture requires four Key Elements of Organisational Function to achieve effective Process Safety Management, namely:
- ANTICIPATION: Recognising and acting on the indicative potential for undesirable events / occurrences.
- ENCOURAGEMENT: Equip employees with appropriate knowledge and embed skill across all areas. Then encourage and support them to rectify pre-cursor issues before they escalate.
- INQUIRING: Ensure that appropriate questions are asked and sufficient analysis is conducted to learn from incidents.
- IMPLEMENTATION: Using systems and work processes consistently and reliably.
Furthermore, there are Four Essential Competencies to ensure the success of this effective Process Safety Management system:
- COMPETENCY 1: Have the conviction to lead safely.
- COMPETENCY 2: Understand how Process Safety works.
- COMPETENCY 3: Develop the ability to influence and encourage people.
- COMPETENCY 4: Retain and practice good leadership skills.
Supervision must also be integral to the development, implementation and maintenance of the programs needed to meet regulatory and internal Process Safety Management requirements.
Supervisors should interface with Operations, Maintenance, Leaders and External Stakeholders to ensure that Process Safety objectives are established, measured and reported. They need to:
- Influence the training and competency of staff.
- Have related authority over Engineers who are responsible for Process Safety deliverables.
- Delegate Process Safety tasks and track performance.
- Be responsible for Process Safety KPIs and ensure review of the Process Safety program.
- Influence and educate other departments and leaders to ensure program requirements are met.
Plant, Process and People
Effective Process Safety Management is essential to the prevention and mitigation of Major Accident Hazards.
However, on its own, it is not enough for reliable Catastrophic Event Prevention. If we reinforce and develop the critical leadership behaviours that drive anticipation, inquiry, encouragement and implementation through all levels, we will create a culture that promotes and maintains Process Safety Management excellence.
This leadership focus needs to ensure that Major Accident Hazards have been effectively identified and that there is understanding of how Loss of Control can occur, along with the outcome of this.
Through this information, the leadership team is able to implement the Major Hazard Control Measures and the Prevention and Mitigation Barriers focusing on Plant, Process and People.
Process Plant Lifecycle
It is essential that the leadership approach to managing focuses across all elements of the Process Plant Lifecycle, and that we recognise within our sector the impact that change has on this lifecycle.
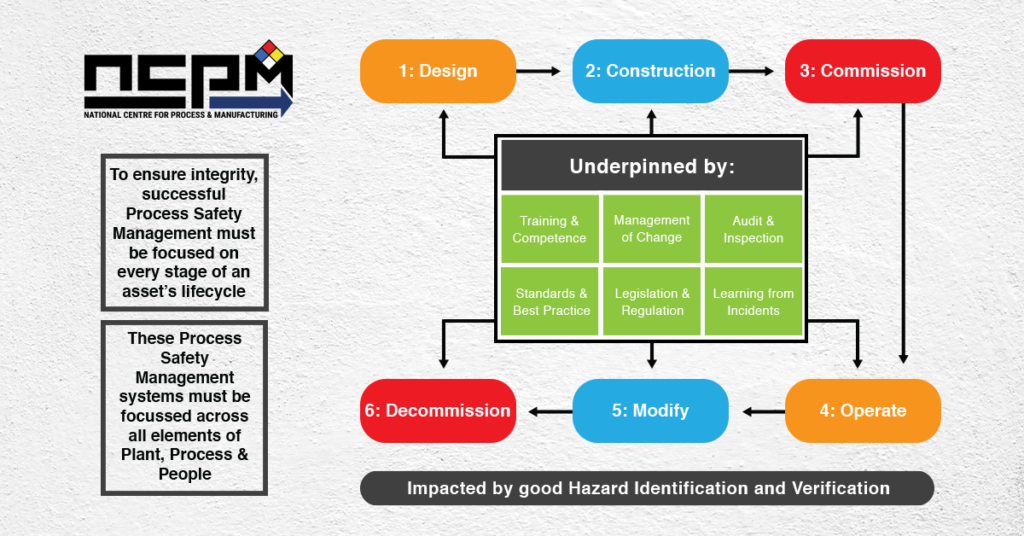
So, as you see, effective leadership in Process Safety Management requires a never-ending and methodical approach; it requires the engagement of everyone on-site, from the cleaning cupboard right up to the boardroom; it requires businesses to be open and honest and to share best practice.
In this way, great leadership can help ensure continued safety for all!
In the next chapter, we will explore the second element of The Big Picture, namely: Hazard identification in the Major Hazard Regulatory Model.
NB: This article contains public sector information licensed under the Open Government Licence v3.0.
Teaching Safety is a Matter of Course
The secret to maintaining good Process Safety – and it’s no secret, really – is ensuring that everyone on your site has had the training they need. That’s as important in the management suite as it is in the process plant.
IOSH Process Safety Awareness Provides learners with the core understanding and awareness of process safety within a high hazard environment and demonstrates how effective process safety underpins safe site operations.
Also, our IOSH-approved Process Safety Awareness and Principles of Process Safety Management courses are the perfect way to ensure that everyone develops the competencies they need to work safely at every level of business.
And our GQA Level 5 Diploma in the Principles and Practice of Process Safety Management course is specifically customised for Supervisors and Management. This course explores concepts around Leadership, Hazard Identification, Risk Assessment, Prevention and Mitigation to confirm systems are working as designed.
So, why not check out our full range of courses and get in touch, today.